A weekend of playing in the sand!
I've just had the most wonderful weekend with other jewellers messing around in what could only be described as a sandpit!
Sand casting is one of the oldest known metal working techniques in the world. It's origins date back to at least 3000 BC and it was the Ancient Egyptians who used this process to make jewellery and tools. The Renaissance saw a revival of it in Europe, and it was used for detailed sculptures, bells, and cannons, such as the famous bronze doors of the Florence Baptistery. The Industrial Revolution brought significant improvements in the process, making it more precise and efficient and modern foundries used it for everything from machinery parts to architectural elements.
The way that it has survived speaks volumes about how effective and versatile it is. Whether it’s creating a delicate piece of jewellery or a robust engine component, I love sand casting because it seems to be a bridge between ancient craftsmanship and modern technology, I like the layer of historical richness it adds to my jewellery making. Its an age old tradition and I love to see those processes still used and in many ways the tools used and the basic principles remain the same as they did in the past.... its about pressing the item you want to cast in metal in to a sticky sand, pour molten metal in to the impression left in the sand, wait for it to cool and then seeing your beautiful creation!
The sand used isn't just sand from the beach, it is a sticky sand made up of very fine sand and clay. It is packed in to some aluminium rings and then whatever you want to cast is pressed in to the sand and the two rings are pressed together. The original item is removed and then you create lots of air vents and a funnel. The funnel is used to pour the molten metal in to the centre of the rings where the impression is and the air vents are so that when the silver is poured in, the air can escape and not prevent the metal from flowing fully in to the impression. Obviously you need a very secure set up for melting the silver and a pretty fierce torch. The melting was thrilling and adrenaline fuelled, but very enjoyable. Once the metal is on a rolling melt, then it is poured in to the mould. Opening up the mould is the fun bit!
Take a look at these photos to show you that process...
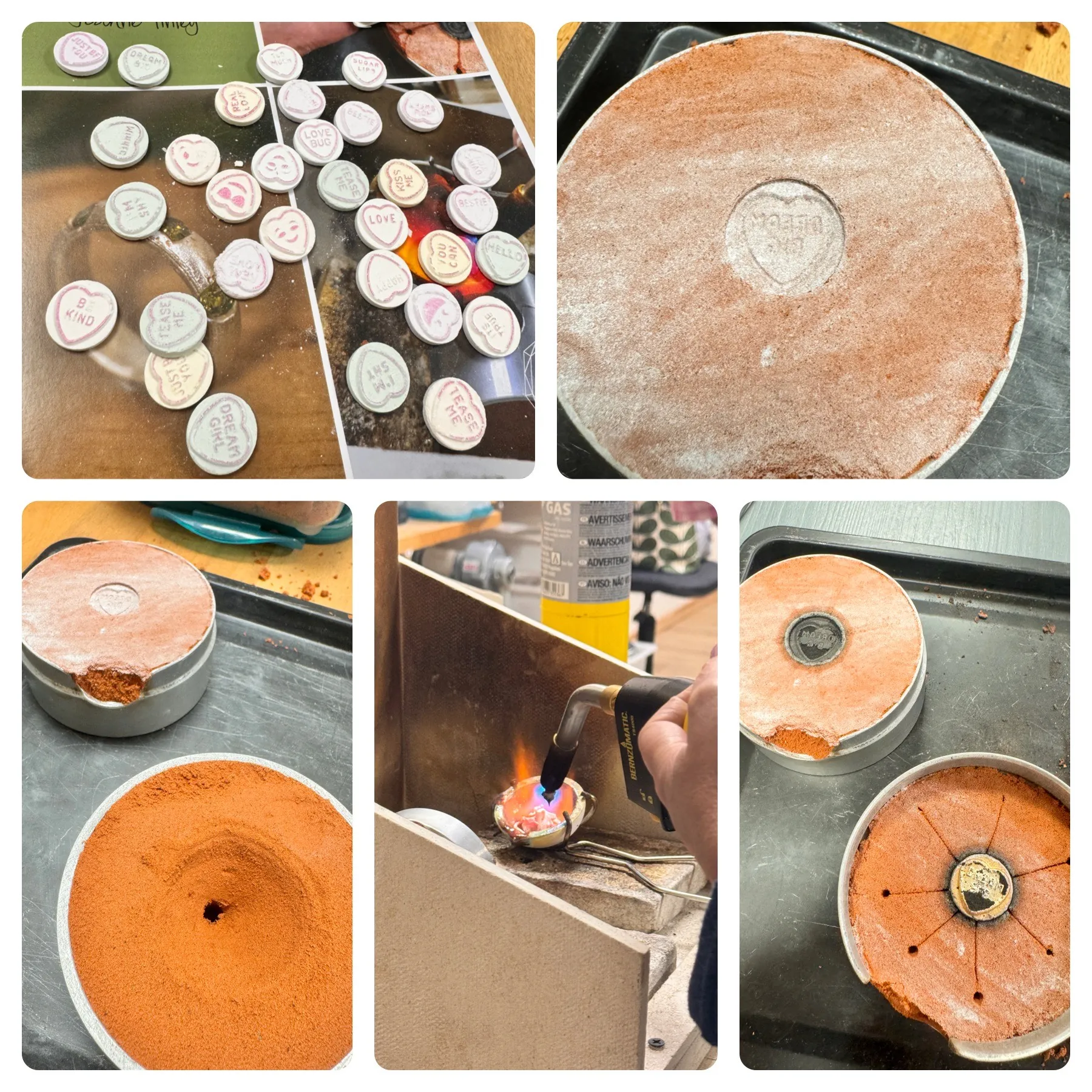
Once cast, there is a lot of cleaning up, filing and polishing to be done. I didn't do that over the weekend as I wanted to cast as many things as I could and practise as many different techniques as possible. I cast some buttons, a love heart sweet, a tiny owl ornament and I experimented with some rough cut rubies and a heat proof cubic zirconia. I also spent most of the afternoon trying to cast a ring. After 5 attempts, I admitted defeat! No matter how many air vents I added, and how many funnels I used, I just couldn't get the molten metal to flow all the way around the ring. I wasn't the only one who struggled with it! I think it will be something I will come back to in time, but for the moment, it is the casting of the buttons and adding the gemstones which gave me the most pleasure.
I'm now on the lookout for some fancy buttons, I've got a new soldering station set up to manage and I'm off to source a really fierce flame! Take a look at all the things I managed to cast over the weekend and keep an eye on my social media to see how they become my next favourite pieces of jewellery...
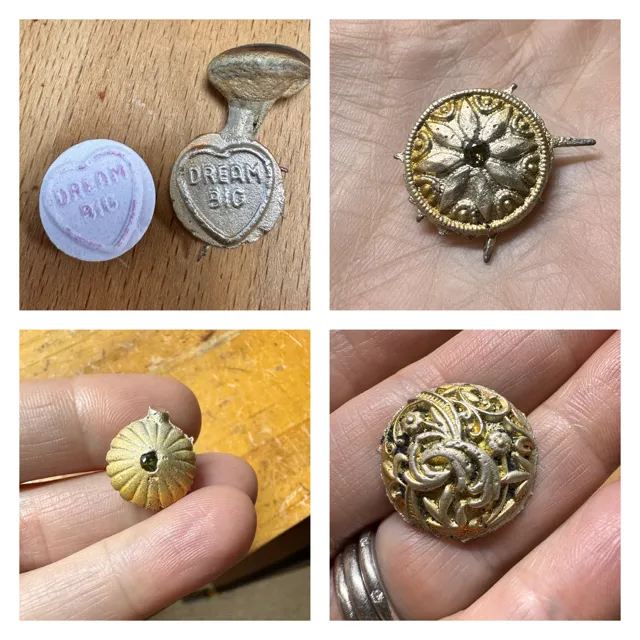